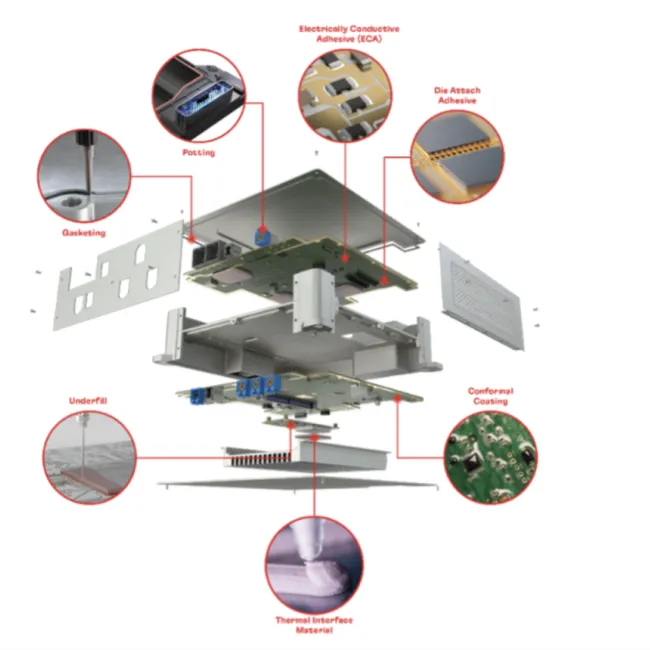
SHERIDAN, WYOMING – Mar. 4, 2025 – As the automotive industry continues to evolve with new technologies, vehicle domain controllers (VDCs) are at the heart of many modern vehicles, consolidating various electronic control units (ECUs) into a single system for improved functionality and reduced complexity. Henkel Adhesive Technologies is leading the way with a wide range of material solutions designed to optimize the performance, reliability, and lifespan of these critical systems.
Optimizing Performance with Advanced Thermal Management
As VDCs continue to grow in computing power and functionality, effective thermal management has become more important than ever. Excessive heat can lead to component failure, shortening the lifespan of the VDC and reducing its overall performance. Henkel offers advanced thermal interface materials (TIMs) to help dissipate heat from sensitive components, ensuring they remain within optimal operational temperature ranges.
“Thermal management is essential for long-term durability and performance,” said Nancy Yang, business development manager for automotive electronics at Henkel Adhesive Technologies North America. “For every 10°C increase in operation temperature, the life of a component decreases by half, which is why our materials are engineered to deliver maximum thermal conductivity.”
Henkel’s curable gel solutions are among the most effective in the market, offering fast dispensing capabilities and thermal conductivity up to 6W/m-K. These solutions help prevent overheating, which could lead to system failures and costly repairs.
Shielding Against Electromagnetic Interference (EMI)
Electromagnetic interference (EMI) is a critical issue as modern vehicles rely on increasingly complex electrical systems, including sensors and communication networks. EMI can disrupt the operation of vehicle domain controllers, leading to errors and system malfunctions. To mitigate these risks, Henkel offers specialized EMI shielding materials that protect VDCs from external interference and ensure that the vehicle’s electrical systems operate seamlessly.
“Henkel’s Bergquist Gap Pad TGP EMI 4000 not only absorbs EMI but also provides thermal management by filling gaps between components and ensuring optimal contact with heat sinks,” explained Yang. “This material is essential in reducing signal disruption, improving reliability, and enhancing the performance of ADAS sensors and other critical systems.”
The TGP EMI 4000 has thermal conductivity of 4.0W/m-K and absorbs electromagnetic energy at frequencies up to 77GHz, ensuring superior protection in high-demand automotive environments.
Increasing Reliability and Durability with Underfill Solutions
Underfill materials play a crucial role in enhancing the mechanical reliability of VDCs by providing support beneath semiconductor chips and other sensitive components. These materials prevent damage caused by thermal cycling, vibrations, and mechanical stresses, ultimately improving the VDC’s longevity and reducing the risk of failure.
Henkel’s Loctite Eccobond UF 1173 is an advanced one-part adhesive designed to provide excellent thermal and mechanical performance. It boasts low viscosity for easy application and quick curing time, ensuring production efficiency without compromising on quality.
“By ensuring uniform distribution of thermal and mechanical forces, our underfill solutions protect critical components and enhance the durability of vehicle domain controllers,” Yang said.
Effective Sealing for Protection and Performance
In demanding automotive environments, effective sealing is crucial to protect sensitive electronic components from moisture, dust, and contaminants. Henkel’s Loctite sealants and gasketing compounds create reliable seals between components, safeguarding the VDC from external environmental factors like temperature fluctuations and vibrations.
“Loctite SI 5972FC is a fast-curing RTV silicone sealant that provides high-performance sealing across a broad temperature range of -40°C to +150°C,” Yang shared. “This ensures that VDCs remain protected in extreme conditions, allowing them to operate efficiently for longer periods.”
Protecting VDCs from Wear and Damage
Henkel’s potting solutions are designed to shield VDCs from dust, moisture, and contaminants, which can otherwise lead to performance degradation or failure. Loctite SI 5035, an alkoxy dual-cure silicone, offers quick curing times and flexible bonding, accommodating the expansion and contraction of materials to prevent damage in sensitive electronic systems.
These potting materials play a crucial role in ensuring that VDCs remain operational in even the harshest automotive environments.
Henkel: Leading the Way in Automotive Material Solutions
As the automotive industry increasingly turns to vehicle domain controllers to manage a wider range of tasks, the role of advanced material solutions becomes ever more critical. Henkel’s diverse range of materials, including products from the Loctite and Bergquist brands, help optimize thermal management, improve durability and reliability, and ensure seamless operation in challenging environments.
“Henkel’s solutions are designed to meet the ever-growing demands of vehicle electronics, providing the necessary protection and efficiency to help VDCs perform at their best,” Yang concluded. “With the continued advancement of automotive technologies, our materials will remain integral to enabling the next generation of vehicle systems.”
For more information please ,visit.